3 November 2022
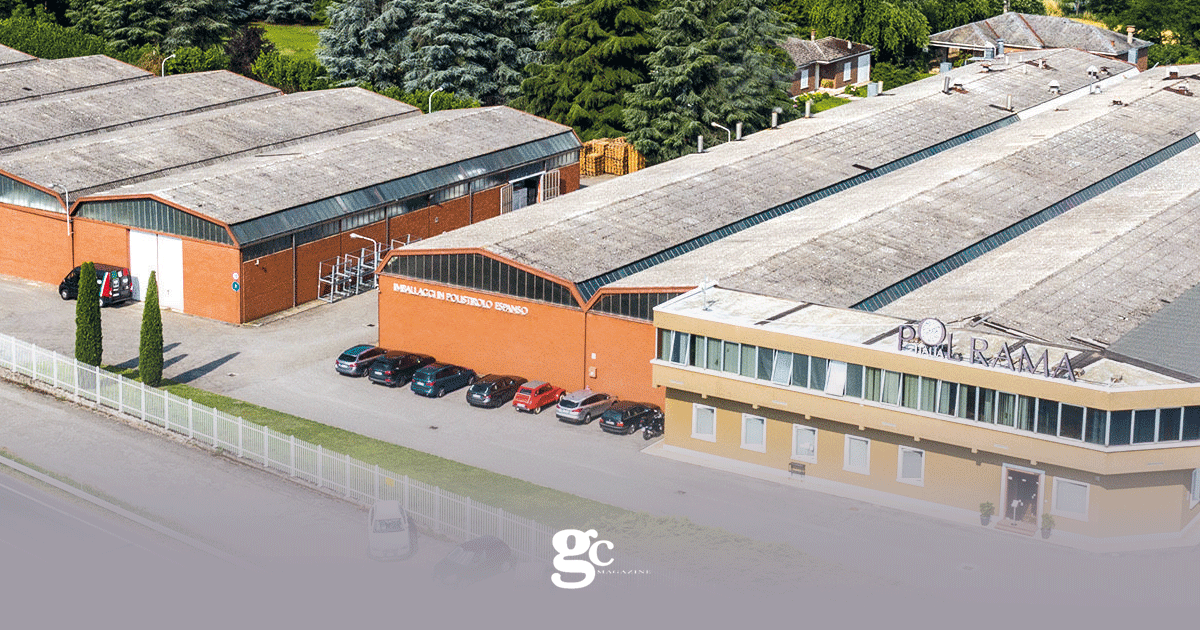
Plastic doesn’t seem to align with the new ecological and sustainable principles we must implement to save the planet. However, for The IES Group, that’s not the case, and they make it clear, starting with their slogan, “We Print Plastic to Save the Planet.” We discuss this with Manuele Lucisano, CEO & General Manager of the Group.
“Printing Plastic to Save the Planet” is our mission, which concretely means implementing every possible action to emit less CO2 eq., not only in terms of production. With the Greta Program, we embrace the entire supply chain and assess the environmental impact comprehensively. For example, an electric car cannot be considered green solely because it emits no polluting gases downstream; the evaluation must also encompass other data such as CO2 eq. emissions during production and end-of-life disposal.
The Greta Program – continues Lucisano – encapsulates our sustainability philosophy, becoming a true brand. We assist forward-thinking companies in adopting this approach based on the 4R rule: reduce, reuse, recycle, recover. We do this following a precise and tested procedure consisting of multiple phases:
First phase: analysis of the company and its production processes.
Second phase: verification of acquired data and preparation of a summary table with corresponding values in Global Warming Potential (GWP), based on internationally established real data.
Third phase: replacing all disposable items with reusable products, if the substitution makes sense in terms of sustainability – both environmental and economic. Sustainability can only be defined as such when it is accessible to everyone and truly applicable.
Fourth phase: after analyzing the materials used, we focus on production processes. It is futile to replace a polluting material with another that is less so if its production requires coal use or involves multiple rubber-based movements.
It is important to understand that, in cases like these, replacement costs more in terms of CO2 eq. emissions than leaving things as they are. Therefore, examining the entire supply chain to minimize movements, maximize automation, and rationalize products is crucial.
To further clarify for those outside the industry, consider a real intervention we made in the HVAC (Heating, Ventilation, and Air Conditioning) sector for a partner who previously used twenty-five components to produce a final product, reduced by us to one. In practice, we operate in all areas that contribute to increased CO2 eq. emissions with the goal of achieving zero emissions.
All these points together enable a true circular economy. With our solutions and materials, we can recover all end-of-life products, regenerate them, and reintroduce them as new products, all certified by an external entity, which is highly valuable for marketing purposes.
Expanded plastics have myriad uses. Thanks to our technical department with over 60 years of know-how, we can integrate our molded products with inserts or pair them with external finishes to achieve a monomaterial finished product that is easily and fully recyclable, with excellent technical, structural, and aesthetic properties.
This allows us to operate in every sector. The IES Group owns specialized brands:
IES Automation, dedicated to industrial and logistics automation.
IES HVAC, for high-performance and lightweight air treatment products.
ELMO, where we are the leading third-party helmet producers in Europe.
Next Design Innovation, dedicated to prototyping and industrializing highly technical products.
IES e-TPU, specializing in the polymer that made Adidas famous with Ultraboost.
Polirama, for food and pharmaceutical isothermal containers.
Among our flagship productions are parts made for ESA’s Cygnus satellite and ongoing projects in the aerospace sector. We take pride in being the first to send expanded polypropylene into space. Additionally, we produce nearly all containers for the famous anti-COVID-19 vaccines.
We have collaborated for years with major industries such as Ferrari, manufacturing molded parts. It is clear that we do not merely print plastic; we assist our clients in maximizing performance, shifting towards different products through Next Design Innovation, contributing to creating and making available systems unrelated to molding.
This is our strength: we are not limited to printing; we offer genuine support to our partners. This ability and freedom to operate across various fields are greatly appreciated by our clients. To illustrate, it’s akin to selling cars without being a single-brand dealership. While a single-brand dealership may have the best brand for them, not being tied to a single brand allows access to all brands and models available on the market, enabling us to suggest the solution that best fits the client’s needs. In doing so, we operate in a win-win scenario where offering the right solution, without constraints, fosters growth for our client and consequently for us. Speaking of win-win, The IES Group recently organized a conference titled “The Qualities of a True Leader.”
A true leader is someone capable of thinking in a win-win mindset, where everyone is a winner. Acting solo or aiming for quick wins does not yield long-term results; achieving real results requires solid foundational work, seeking feedback, and accepting constructive criticism.
A leader must have the courage to make tough decisions, taking on the risks, knowing the fundamental importance of the team of professionals built around them, who share their values and mission: printing plastic to save the planet. Thus, plastic and the environment…
We firmly believe – concludes Lucisano – that the solution is not to stop producing plastic but to adopt virtuous behaviors while doing so. At The IES Group, we use only energy from 100% renewable sources. We have invested €1.5 million to replace all steam generators, LED lighting fixtures, all to ensure energy efficiency.
The IES Group
Via Cimabue 16 – fraz. Montesiro, Besana in Brianza (MB)
www.theiesgroup.it
Taken from Green Company Magazine (Volume 8) – see all magazine issues
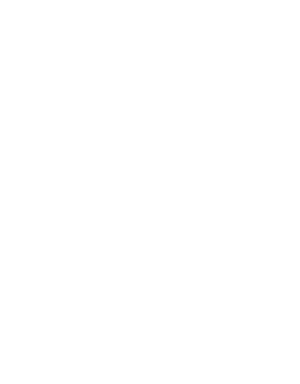
Press review
For information
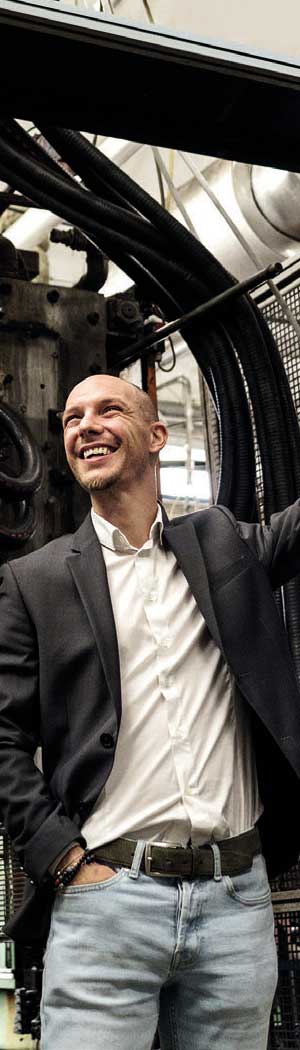
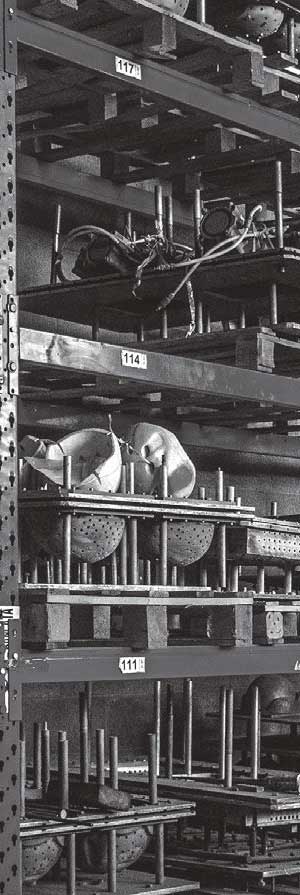
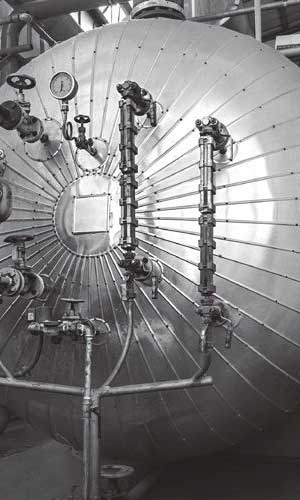